Productivity & Agility
Connected Workers do it right first time, safely and efficiently
Digital shop floor workflows in Zaptic speed up information flows, free up non value added time, and drive loss eliminating action at scale.
Request Demo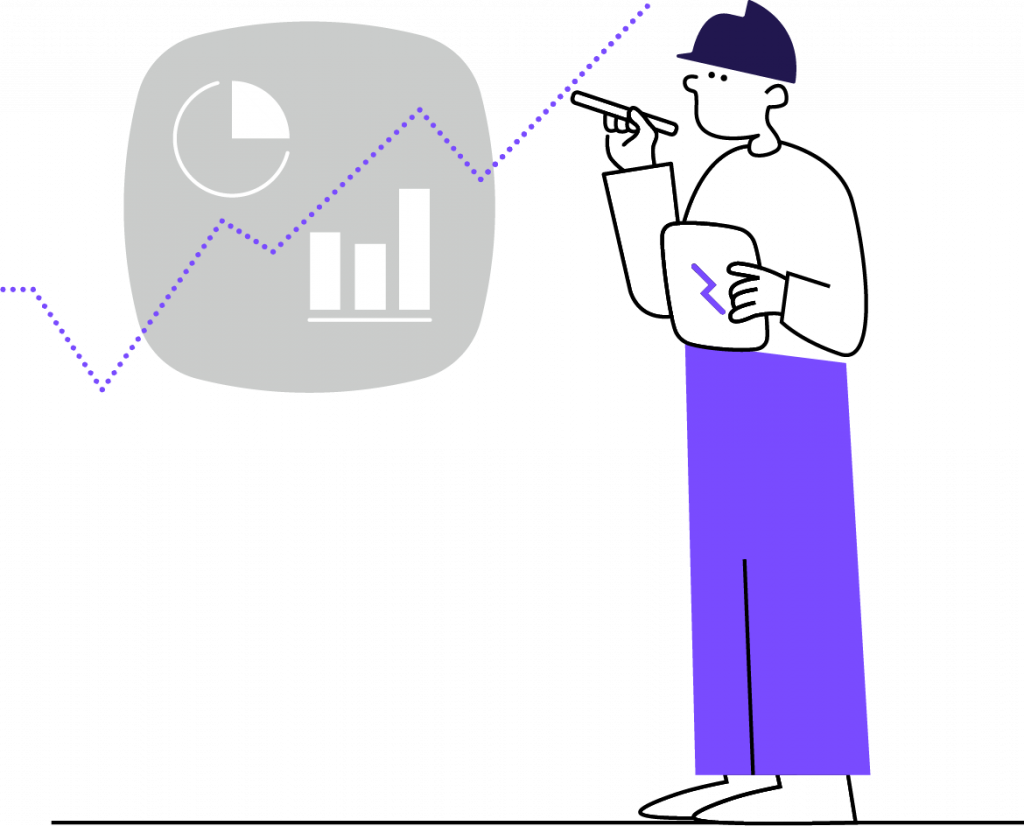
The Problem
Our Solution
A heavy reliance on paper, spreadsheets and tribal knowledge in daily shop floor operations holds back too many manufacturing teams.
Bottlenecks caused by information and knowledge gaps constrain capacity utilisation, exacerbated by increasing rates of employee turnover and new product development.
Zaptic provides a no code platform to digitise daily management systems with work instructions and work order software.
Frontline teams are guided on what to do, when to do it and how to do it, supporting full productivity even with constant change in your processes and workforce.
Example use cases: Autonomous maintenance; Defect Handling; On-Line Quality checks; Centerlining; Changeovers; Gemba Walks; Safety Observations; Shift handovers; Checklists, audits and more
Best practice templates or drag and drop configuration of your own workflows.
How Zaptic Helps
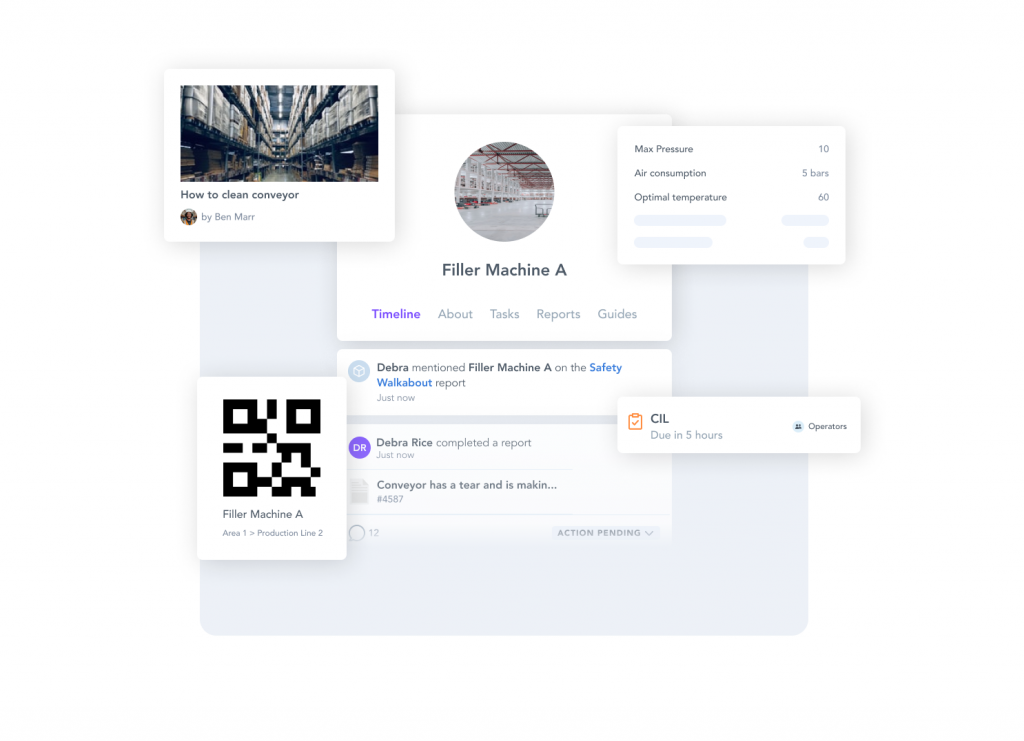
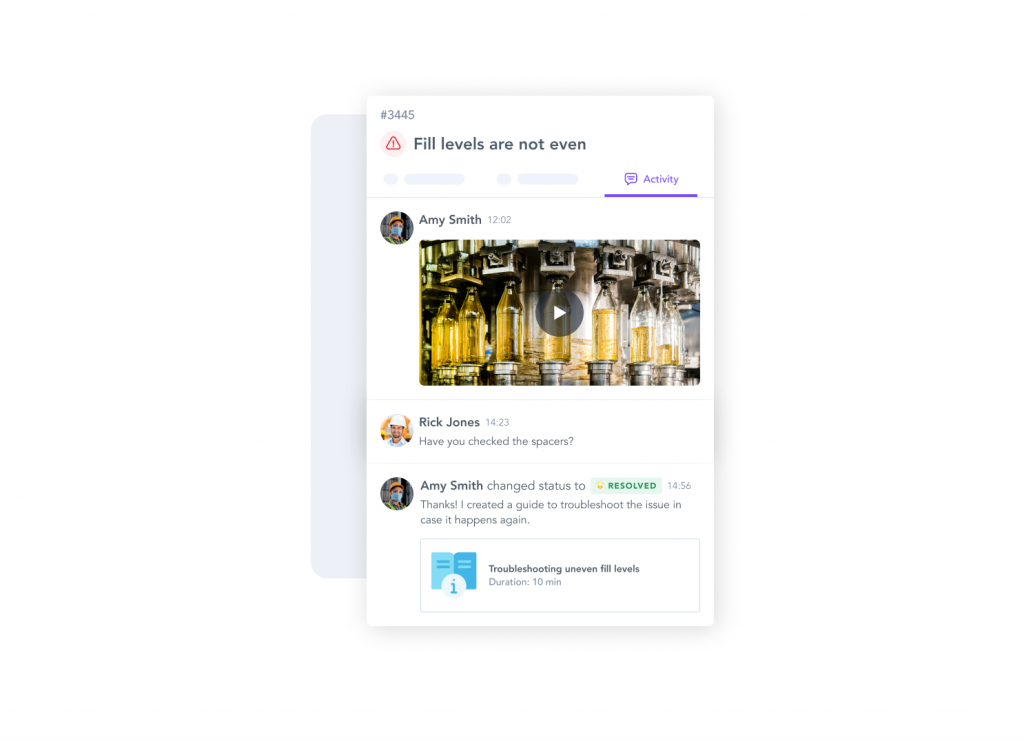

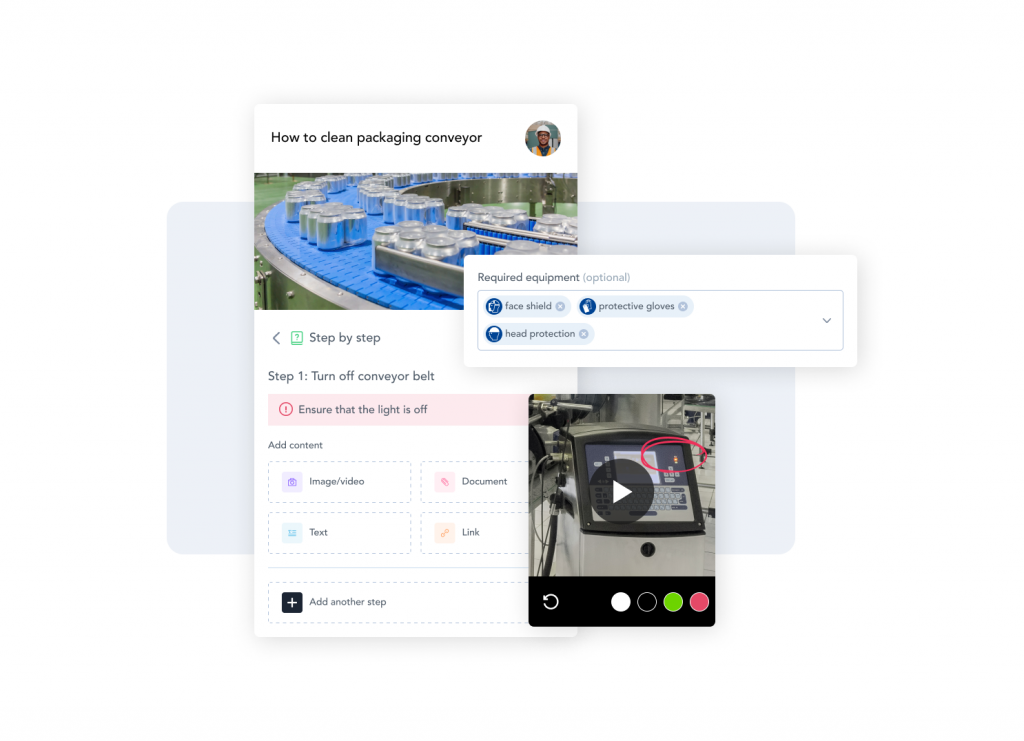
Operator Autonomy
On the floor access to work instructions via scan or search within the connected worker solution.
Capture and escalate defects with rich media directly from the place of work.
Integrate with machine and production data (e.g. MES, historian), to push the right checks and work instruction, to the right user, at the right time.
Shop Floor Collaboration
Capture, visualise and track all issues and actions on Zaptic’s daily management boards to aid communication between shifts and speed up problem solving with electronic work instruction.
Event based communication streamlines collaboration between production teams and support functions to aid troubleshooting, repairs and day to day problem solving.
Build escalations workflows to automate, streamline and standardise issue resolution cycles.
Process Traceability
Digital workflow timelines provide visibility on what’s been done, by who and when, with conversation history and multimedia.
Process metrics and analytics boards highlight improvement and savings opportunities.
Automated audit trails ease inspection preparedness.
Knowledge & Best Practice Sharing
Deliver work instruction to workers in the flow of their work, by linking guides to digital workflows.
Capture, retain and organise knowledge by enabling workers to create guides (e.g. OPLs, troubleshoots etc) in an easy, social media style experience directly from the place of work.
A searchable database of previously resolved issues supports workers encountering similar issues.
The Results
The Results
250
Paperwork Hours Saved Per Week Per Site
Paperwork Hours Saved Per Week Per Site
11%
Overall Equipment Effectiveness Improvement
Overall Equipment Effectiveness Improvement
200%
Faster Issue Resolution
Faster Issue Resolution






Digital Transformation
Put your people in control
Zaptic’s no code approach accelerates and promotes shop floor digitalisation without expensive changes to equipment processes.
View Challenge